Job vs Process Costing Transcript
Costing Methods > Job vs Process Costing
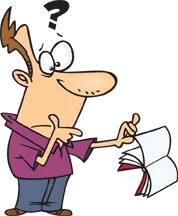
One of the most important responsibilities of Managerial Accounting is determining accurate product costs. You can imagine how difficult it would be to price products appropriately or determine production volume levels, without knowing the cost of a product. In fact, I worked for a small produce company once that had this very problem.
There are two primary ways product costs are determined; job costing and process costing. And when we talk about product costs; remember, we are talking about direct materials, direct labor, and manufacturing overhead - an indirect cost.
In the job costing system these material, labor, and overhead costs, are assigned to each job or batch. A job or batch has its own distinguishing characteristics like unique or custom products or customer specific products. The cost object is the cost of the job which which could include one product or a batch of identical products.
This slide shows graphically a couple of items that tend to be job costed - wedding invitations and menus are unique products specific to a particular customer.
Process costing is used when a large volume of similar products are manufactured. Costs are accumulated for a period of time, you know, a week or a month rather than for a set job. Costs are assigned to departments or processes for this specific period of time. If process costing has several activities like mixing, bottling and packaging, costs are added at various times throughout those activities.
This slide graphically shows an item that tends to be process costed.
DVDs, or any other generically mass-produced item, would be a process costing.
You'll have an opportunity to learn about the accounting for both job and process costing in this video series.