Inventory Methods
Inventory Methods
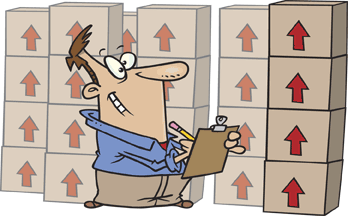
Inventory Methods
There are two basic methods of accounting for merchandise inventories which are called Periodic and Perpetual. Just the definition of the terms perpetual and periodic should trigger a pretty good idea of what the two basic methods actually are. Periodic means occasionally and perpetual means continually.
Periodic Inventory System-Simple method for keeping up with products and calculating the cost of products that were sold in a period and requires a physical count at specified times normally the end of an accounting period and at the very least a count must be made at the end of your accounting year in order to be able to calculate the cost of items sold and the cost of items still on hand.
Perpetual Inventory System-Method for keeping up with products and calculating the cost of products that were sold in a period. Up-to-date inventory records are continually maintained at all times. A detailed record (subsidiary ledger record) is maintained for each product that keeps up with the quantities and cost of each purchase and the quantities and cost associated with each sale. An actual count is usually done at the end of the year in order to check the accuracy and correct any errors in the detailed records.
Taking The Inventory
You've probably heard people use the phrase "taking the inventory". What they are talking about is actually performing the physical count of the inventory.They may have even used some four letter adjectives with the phrase. Why would they do this ? The time, cost, planning, and effort involved in taking an accurate inventory can be enormous. In other words it's a hassle, but it needs to be done. As I was always told as a kid, "a job worth doing is a job worth doing right".
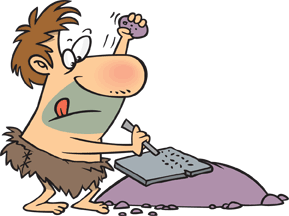
How much time, cost, planning, and effort is required ? It depends. Mom and Pop Shops that maintain a small selection and quantity of items on hand don't require as much as say a company like General Motors. Is there any way to help minimize the effort required ? Many businesses take an inventory at a time when the amount of stock on hand is at a low point. Makes sense to me. The less I have to the count, means less time, cost, planning , and effort is required.
When do I do the count ? Some businesses are able to count during normal business hours while others might count at night or during closed times or even close down to take their inventory. Again it depends on your type of business and the effort required. Some businesses even hire inventory service businesses to do the count for them. You've probably seen these people with their machines in grocery stores.
Are there any special forms I should use ? Yes, a count sheet and possibly a cost calculation form but you can design them yourself.
What information should I include on my count sheets ?
- General Information
- Department/Area
- Counted By
- Sheet Number/Reference
- Date of Inventory
- Extended By
- Stock/Item Number
- Description of Item
- Bin/Location
- Unit Of Measure
- Quantity On Hand (Counted)
- Costing Method
- Unit Cost
- Extended Cost
Or
Reference to Cost Calculation Sheet - Notes/Comments- such as condition of items
- Total Sheet Cost
Do I need to take any Special Precautions ?
Only the goods that actually belong to the business should be counted. Merchandise that you have on consignment does not belong to the business and should not be included as a part of your businesses inventory although the supplier may require you to count these items and report the count to them. For those that don't know, a consignment occurs when a supplier maintains title/ownership of the goods but you have custody of the goods and are allowed to sell them and pay for the goods as they are sold. On the other hand, if you have supplied other businesses with consigned goods you need to count or make arrangements to have a count performed and include your consigned goods in your inventory.
Only the goods that actually belong to the business should be counted. Merchandise that you have on consignment does not belong to the business and should not be included as a part of your businesses inventory although the supplier may require you to count these items and report the count to them. For those that don't know, a consignment occurs when a supplier maintains title/ownership of the goods but you have custody of the goods and are allowed to sell them and pay for the goods as they are sold. On the other hand, if you have supplied other businesses with consigned goods you need to count or make arrangements to have a count performed and include your consigned goods in your inventory.
Merchandise that has been sold but not yet delivered is a sale and should not be included in your count.
Merchandise that you have received and have title to but have not processed such as goods waiting to be unloaded or in a holding area waiting to be processed in should be processed and included in your inventory count.
A procedure for identifying what has and has not been counted such as tags on the merchandise counted or any other method or procedure that tells you whether the goods have been counted should be used. This makes sure that goods aren't omitted from the count or included more than once.
Assigning Costs To Inventory
Counting our inventory is only half the battle. We also need to assign costs to all the items we still have on hand. If all our purchases of a specific item were made at the same unit cost, we could easily arrive at the cost to use for valuing our inventory. We all know though that this is normally not the case. So our problem becomes what cost do I use to value my inventory when my business has made purchases of the same item at different costs.
Counting our inventory is only half the battle. We also need to assign costs to all the items we still have on hand. If all our purchases of a specific item were made at the same unit cost, we could easily arrive at the cost to use for valuing our inventory. We all know though that this is normally not the case. So our problem becomes what cost do I use to value my inventory when my business has made purchases of the same item at different costs.
Example
Product: Super Widget
Purchases:
Product: Super Widget
Purchases:
Quantity Unit Cost
100 $10.00
300 $9.00
200 $11.00
Do I use $10.00, $9.00, $11.00 ,an average or what to assign cost to my ending inventory ? Don't jump the gun and get excited yet. This problem will be discussed later. I just wanted you to be aware that coming up with the proper cost to use in valuing your ending inventory requires your business to make some assumptions regarding costs.
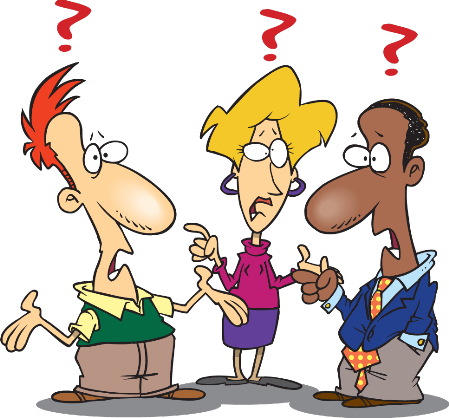
What's Next ?
Periodic Inventory Method